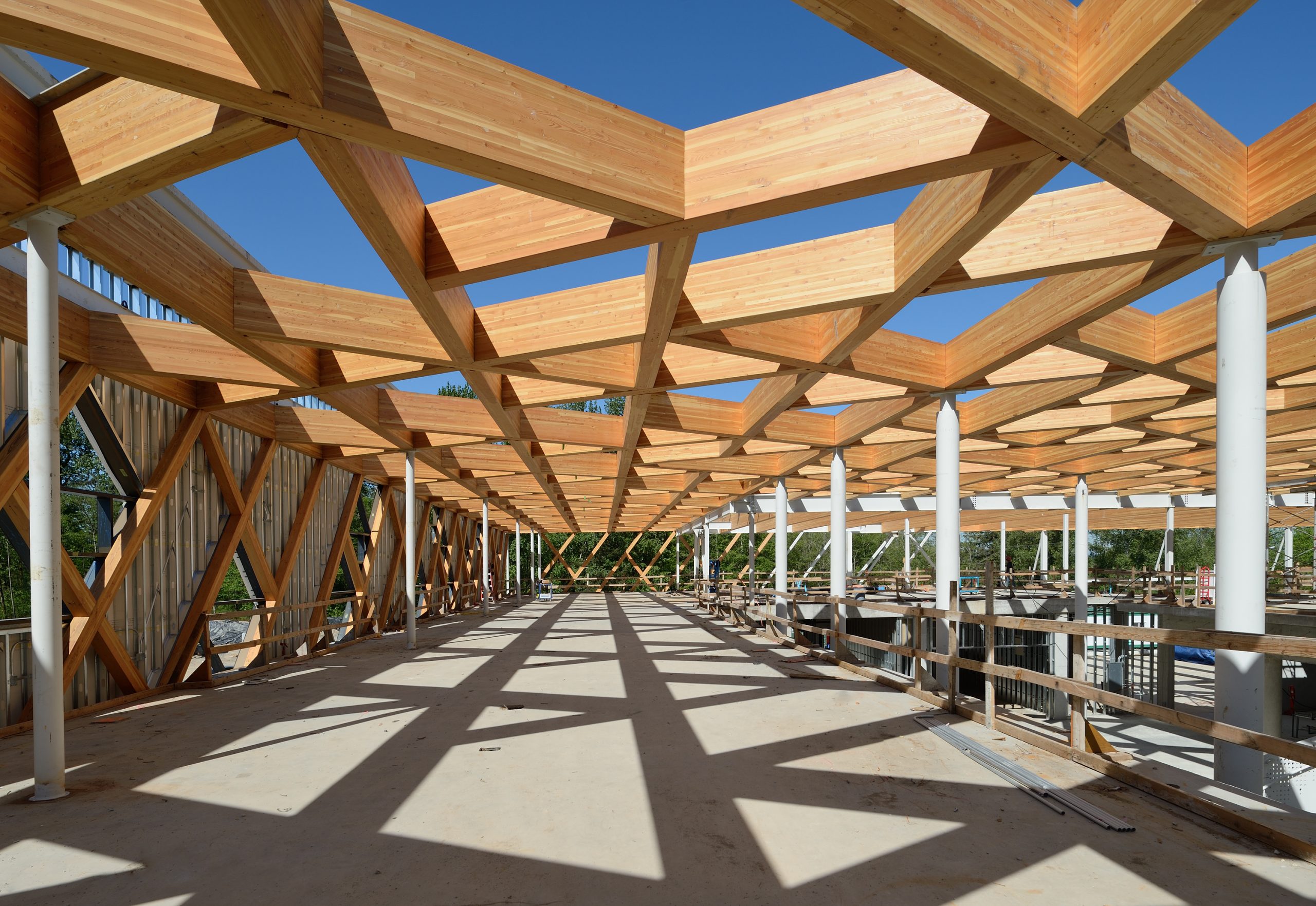
15 Dec Mass Timber: An Interview with RJC’s Leon Plett and Terry Bergen
We sat down with Leon Plett and Terry Bergen, Managing Principals at RJC’s Victoria office, to discuss an area of increasing interest to business leaders in AEC industries: mass timber.
Image (above): The Clayton Heights Community Centre, currently under construction in Vancouver, employs a two-way wood system that allows the structure to span to discrete column locations without the need for drop beams. Architect: HCMA Architecture + Design. Engineer: RJC. Image courtesy RJC and Michael Sherman Photography.
RJC foregrounds a strong commitment to sustainability. When and how did the firm transition into working with mass timber?
Leon: Mass timber is actually nothing new. I think that North Americans, especially on the west coast, have been familiar with timber construction and it’s many different forms for a long time. Manufactured mass timber is just the latest advancement in technology.
So maybe the question is when did we transition from building with single pieces of lumber to what we now consider mass timber. It’s been an evolution in manufacturing. There are many engineered lumber components that we’ve been familiar with for a long time, but the manufacturing of large panels like cross-laminated timber (CLT) has really changed the game. That, in tandem with the development of CNC machining technology and Building Information Modeling (BIM), has allowed us to see early building models translate directly into shop drawings that are then produced in off-site facilities rather than on-site. And that’s been a big change.
RJC’s adoption of mass timber has come out of our desire to find the best solution for the client and their building. We’ve never been “only concrete people” or “only steel people” — we’re always looking for what we think is the best material for a given the client’s site and program, and weighing it against external variables like marketplace availability and price. Mass timber just ticks so many boxes. I think that’s why we’re seeing more and more of it.
Terry: From a building enclosure perspective, timber has always been another aspect of the building that we’ve wanted to protect from the environmental elements — moisture, heat, vapour transport. Up until recently, we’ve always followed the lead of the architect and structural teams and designed for whatever systems best meet the needs of the building and the client. Now there’s a much greater appreciation for the embodied carbon advantages of mass timber and the need for better building science.
Does CLT offer any advantages from a weather perspective?
Terry: In some ways it’s actually the opposite. You need to be more careful in terms of managing the exposure of mass timber to the elements throughout the assembly process. The industry has started to appreciate those risks over time and learned how to manage them appropriately. It’s been a bit of a learning curve, particularly out here on the west coast where it’s very wet. It’s almost easier to manage mass timber builds in colder climates where you can blow or brush off snow instead of contending with 100 millimeters of rain per week.
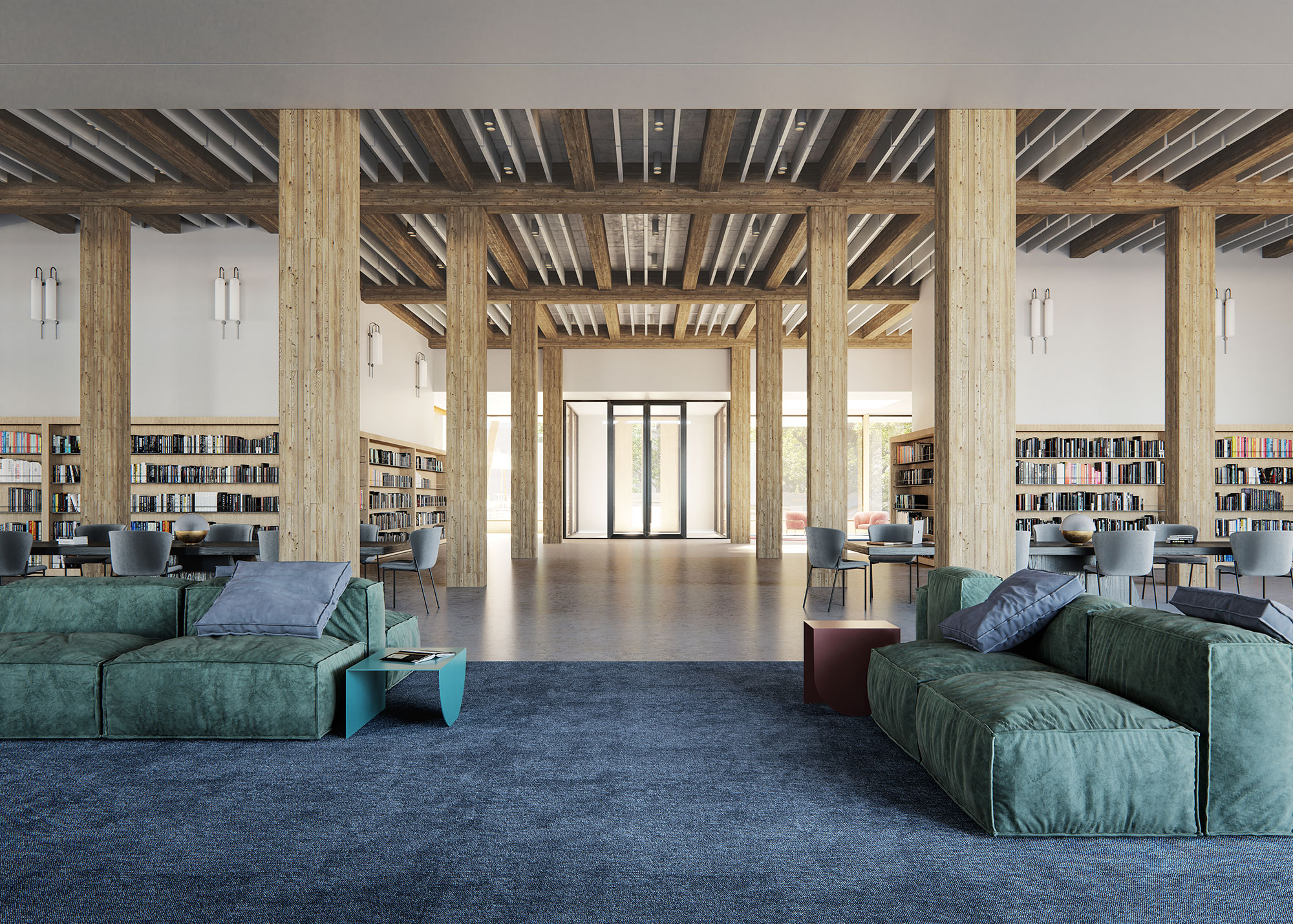
Esquimalt Town Square in Victoria is a mixed-use project that blends residential low-rise towers, office, and commercial space, and features a four-storey mass timber library (pictured). Architect: D’AMBROSIO architecture + urbanism. Engineer: RJC. Image courtesy Aragon Properties Ltd.
How have any of your working methodologies with architects, developers, or construction consultants changed in the context of advances in building systems and mass timber?
Leon: With advances in BIM, our workflow has changed significantly in the last 10-15 years. We’ve seen a significant increase in design details and the amount of decision-making in the very early stages of a project because you can now render a 3D model of a building instead of working from plans like we did in the old days. BIM has set a new standard. Our buildings have become more complex and our modelling tools more powerful; as a result, client and contract expectations are much higher. If you look at plans for buildings 75 years ago, there would be maybe 20 sheets of architectural plans. Now, for the same project, you might have 150 sheets.
When it comes to mass timber, the workflow is dictated by the manufacturer’s capabilities. With a concrete building, architects and engineers can design whatever we want, as the formwork is custom for every project. With a mass timber building, we are limited to the panelization that a fabricator can manufacture, their CNC capabilities, crane loads, and access on site when we’re in the assembly phase. All of those variables on the component side limit what we’re able to do. It’s like working with Lego versus Playdough. If you’re working with Playdough, you can build whatever you want; there’s no limitation. When you’re working with Lego, you have a set number of shapes and sizes in the box and your creativity is bounded by the material.
Terry: With a high-rise, it may be the case that we have a composite building with a concrete core and wood columns and floors. The structural design will set the tolerances for movement and shrinkage, and therefore determine the material systems and suppliers. Once a supplier is in place and the structural design is finalized, the enclosure design can begin. From an enclosure perspective, it’s about working with the properties of those pre-assembled materials and developing a design that will accommodate the movement and shrinkage tolerances associated with a given system. Whether it’s a traditional curtain wall or a panelized wood approach, you’re still working to the inherent material properties of that medium and what manufacturers can supply.
Throughout the entire process, it’s a very integrated discussion with the client, construction manager, and larger team of consultants, whether it’s about the protective coating system, on-site versus off-site fabrication, site logistics, or carbon density calculations.
In your experience as engineers, what are some of the biggest hurdles to working with mass timber today
Leon: The adoption of new regulations has been relatively slow. Even though we’re capable of designing 30-storey timber towers, building codes will not allow it. The cycle for updating codes and requirements is long, and right now local municipalities have to approve things and are perhaps — by no fault of their own — not as familiar with what mass timber is yet. As a result, it can take time in smaller markets to ensure officials are familiar and comfortable with what we’re proposing.
A lack of competitive pricing is also a challenge, as there’s still a limited number of suppliers. With steel and concrete, there’s no shortage of suppliers, but there are only a few large suppliers of mass timber in British Columbia. Beyond that, we’re looking to the States, Europe, or eastern Canada, which adds shipping costs and changes the carbon equation.
RJC is very active with the Canadian Wood Council and various code development initiatives. Can you speak to this work?
Terry: I am a member of the ASTM’s Committee E60 on Sustainability, which is a consensus standards committee that looks at sustainability broadly and holistically. This includes considering materials such as mass timber from a comprehensive perspective: embodied carbon, harvesting, manufacturing, and transport. It’s an ongoing improvement and learning process to help raise awareness and standardize these calculations across the industry. ASTM has a global reach, so the goal is to have countries around the world adopt these standards.
Do you feel like you’ve been able to play a role in educating decision-makers on the benefits of mass timber or influencing the trajectory of regulatory bodies with respect to code?
Leon: Some of that happens at a project level. There have been some projects in Victoria and the surrounding region where we’ve worked with local authorities to go beyond what the building code permits. So yes, we’ve been able to secure these approvals in a local context, and when that happens it helps to push the limits of provincial and national codes as well.
Engineers — and RJC — are just a subset of partners in the industry who are advocating for mass timber. We see a lot of buy-in from architects, developers, and institutions, all of whom recognize the benefit. When talking about the code cycle, it’s not that anybody in particular is pushing back against regulating the use of mass timber. It’s just a slow game. Extending combustible construction from four to six stories was only two code cycles ago, so it’s very recent, as was the decision to allow mass timber buildings of up to 12 storeys in Canada. Our job is to try to anticipate these changes in the code alongside code consultants. We are lucky to work with some of the best code consultants in Canada who help us overcome regulatory hurdles where we aren’t necessarily meeting the prescriptive requirements of the code, but are nevertheless meeting the intent.
Terry: Provincial and regional governments are also quite supportive and on board. In British Columbia there’s the Wood First Act, which encourages the use of wood in all aspects of construction. Regionally, there’s also an appreciation and desire to use those particular materials. Vancouver Island has a history of being a forestry-dependent economy. And while this isn’t necessarily true today, this “wood-first” culture still remains. There’s a real real desire amongst clients to support the advancement of mass timber.
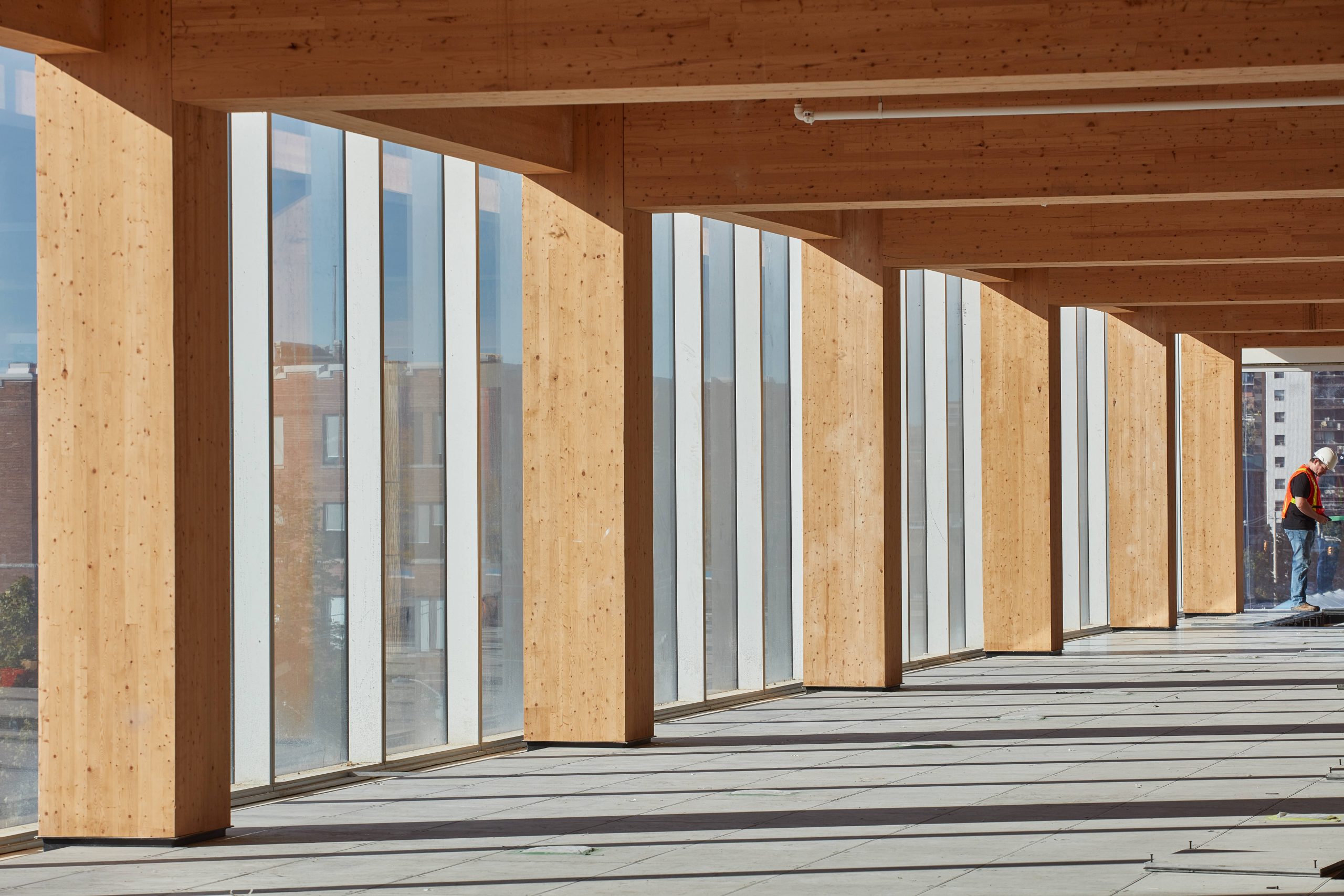
The interior of 80 Atlantic Avenue, a five-storey building in Toronto that showcases mass timber structural elements throughout the upper floors. Architect: BDP Quadrangle. Engineer: RJC. Image courtesy RJC.
Are there things that we can do with mass timber today that we couldn’t accomplish even five or ten years ago?
Leon: Absolutely. Five or ten years ago, we were not permitted to build combustible buildings taller than six storeys. We’re now able to build combustible structures up 12 storeys. That’s a huge change.
Have there been advances in particular kinds of laminated wood?
Leon: We’ve had CLT for a number of years, but the manufacturing capacity and capability has changed over time. New manufacturers are entering the arena, and new options are coming to market — mass plywood, dowel-laminated timber, etc. The biggest advancement is that cost has decreased dramatically to the point where mass timber is now cost-competitive with conventional concrete and steel for 10-15 storey buildings.
How has mass timber helped move the dial on advances in building science?
Terry: From the perspective of building science, advancements have been on the material side of things. Overall, there’s a greater understanding of how to treat the material appropriately — keeping it warm, comfortable, and dry — especially during the construction process.
Before the development of CLT panels, we were seeing a lot of nail-laminated timber (NLT) systems, which lead to issues during construction, like moisture contamination, that inevitably require downstream repairs. CLT has helped to address these issues, but the industry as a whole has also developed a better understanding of optimal conditions for mass timber during construction, fabrication, and installation.
Now, with the cost of mass timber decreasing, not only can it be leveraged for its aesthetic qualities, but also used throughout the building as a primary structural system element, which can lower the embodied carbon overall. From the standpoint of a material science advancement, this can really help our long-term environmental footprint.
What are some of the most common misconceptions you encounter when it comes to mass timber?
Leon: The big one we hear from clients and authorities is the worry that these buildings will catch fire easily. That said, it doesn’t take long to put someone at ease with respect to those questions. Much research and fire testing has been conducted that clearly demonstrates how mass timber chars and protects itself. It’s very easy to understand that in the context of modern building codes, structural systems, and sprinklers, tall timber buildings are very safe.
Terry: Fire is generally the biggest misconception, but cost has traditionally been a concern as well. Advances in manufacturing are helping to address that, though. Now it’s mostly a supply issue: everyone wants to use mass timber and you can’t get enough of it.
Do you find that there’s anything that surprises clients when they adopt mass timber? Does it subvert certain expectations?
Leon: It actually tends to be the opposite. Clients typically come in excited with high expectations of what mass timber can do. People have a lot of confidence that it’s going to solve many of the problems that plague the construction industry. But buildings are still buildings; foundations are still foundations; and getting out of the ground on a tough site will always be a challenge. Mass timber can help us in a lot of ways — we can design buildings that are lighter, require less foundations, and perform better seismically. But that’s not to say we won’t encounter similar hurdles with wood as we would with other materials.
Terry: In terms of managing expectations, clients would love, for example, to use engineered wood products as cladding on buildings. It’s clear that we can get around the whole combustibility issue, but managing the installation process — and moisture contamination in particular — requires an additional level of diligence and caution throughout the construction process. Until we have the ability to actually physically install these systems and components on site with a high degree of knowledge and repeatability, and are able to adequately manage the moisture issues, there remain limitations. We would all love to use wood all the time, but we also have to work with clients to help them understand that there are other considerations to address and sometimes other materials are a better choice to meet their goals.
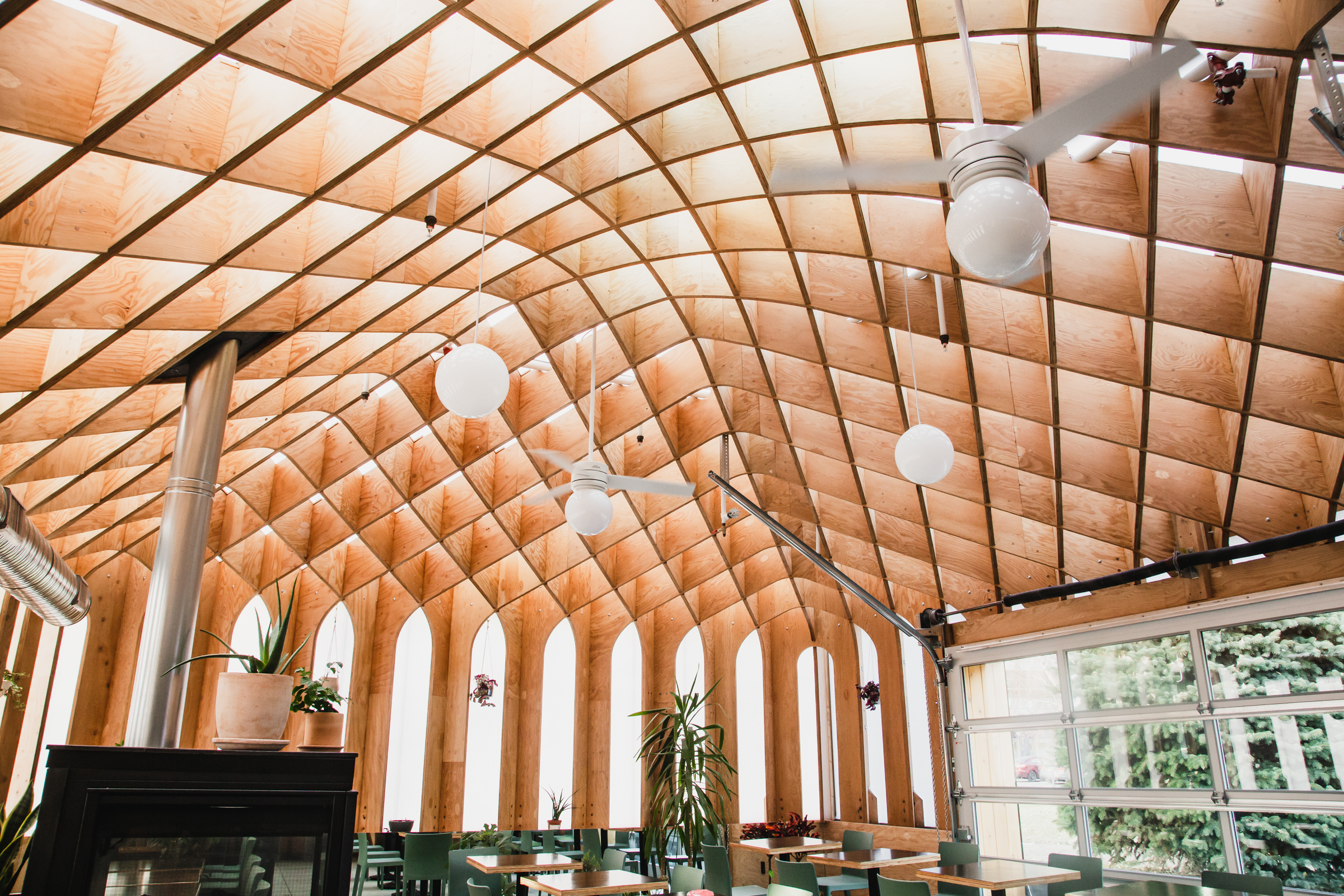
Interior of Sidewalk Citizen, a restaurant in Calgary that earned RJC Engineers a 2020 Prairie Wood Design Award. Architect: Studio North. Engineer: RJC. Image courtesy Haptic Patina.
What role does the prefabrication of mass timber components play in helping to resolve building enclosure issues?
Terry: When you talk about traditional glass or aluminum curtain walls, you have a myriad of system suppliers around the world to source from. These manufacturers are developing products in climate-controlled environments that are then assembled and shipped to site. The CLT industry is only in the very early stages of that and many projects are still prefabricated on-site. One of the big logistical challenges experienced by our construction partners is figuring out where they can put a temporary shelter or warehouse to build enclosed components on-site. Solutions to this are being worked out quite quickly. A number of R&D and product supply companies have emerged in the past few years, but they’re still fairly new and actively working through these challenges.
Is RJC part of any R&D working groups that produces or publishes research on mass timber?
Leon: We have a number of industry and approval authority partners with whom we’re currently working. We partner with universities to do research and testing in their labs; with manufacturers and fabricators assessing components and connections; and with European suppliers to help secure North American approvals for their processes and materials. Here in Victoria, we designed a 6,000-person soccer stadium that was built entirely from timber manufactured in Italy. For this project, we worked directly with the Italian engineers to secure the approvals to build with their timber in Canada. We’re really collaborating with people across all facets of the industry to move wood forward.
What are some of the opportunities we have yet to take advantage of when it comes to mass timber?
Leon: We’ve just begun to scratch the surface of mass timber. The greatest opportunity lies at the intersection of mass timber and off-site fabrication. We finally have a material that can span a long distance and is panelized, making it easy to use with CNC machining equipment. So I think we’re going to see much more off-site manufacturing of buildings in much larger components — not only façades, but also floors and primary structures. Regardless of prefabrication capabilities, the majority of buildings are still built on-site, in the mud and the rain, when they could be built in a climate-controlled factory.
From a code and environmental perspective, there’s definitely more R&D that can be done to truly take advantage of the embodied carbon benefits of mass timber. There will always be a place for concrete and steel, but using engineered wood products to suit the same needs while reducing the carbon footprint of a structure will be a key piece in helping us meet our 2030 and 2050 goals in terms of carbon reduction.
Where do you situate yourself on the spectrum of being “wood purists”? How do you feel about hybrid approaches to building?
Terry: A lot of it is project-specific. If all things were equal, we would always opt for the lower carbon product, which is typically wood. But that’s not to say there haven’t been advancements with other materials with respect to the use of recycled content, innovative carbon capture, and cement replacement materials. If I could default to one material, yes, it would likely be wood for most buildings and the majority of their components. But everyone understands that as an industry we have to do better. Hybrid approaches often provide the best lifecycle performance for a building with respect to durability and resiliency, so it’s important to be mindful of advancements in all materials, components, and assemblies.
What exciting projects is RJC working on right now?
Leon: Tall timber high-rises are top of mind for RJC right now. We’re working on a number of mass timber residential projects in the 12-storey range. Mass timber provides the benefit of a lighter structural system and reduces the seismic load. Because of that, we’re able to erect buildings on difficult sites with challenging soil conditions. These buildings are lighter than comparable steel and concrete structures.
British Columbia is also a great place to work with timber — it doesn’t take much to get developers, planners, cities, and the public on board in a big way! This is why Esquimalt Town Square is so exciting to me. People drive by and take pictures. I think there’s something special about a mass timber building going up that’s not quite the same as concrete and steel. Now it’s just about getting more of these projects out of the ground.

Tresah is Victoria’s first mass timber condo development. The 12-storey tower will be constructed using cross-laminated and glue-laminated timber. Architect: D’AMBROSIO architecture + urbanism. Engineer: RJC. Image courtesy Speed & Frances.